Influence of cutting and punching on the magnetic properties of electrical steel
Sheets and strips from electrical steel are delivered in the finally annealed (DIN EN 10106, 10107) or in the semi-processed state (DIN EN 10126, 10165).
Laminations of finally annealed electrical steel are directly manufactured after punching to magnetic cores in general.
Semi-processed material after punching is annealed in general. During this annealing the deformed lattice structure (including the punching edge range) of the punching laminations recrystallizes.
The excellent magnetic properties are an argument for the use of this “semi-finished” material in particular in cases, in which the specific punching edge length [m/kg] and the relative percentage by volume of the punching edge range are high.
Magnetic properties can be improved by
- a reannealing of the punched parts from a finally annealed electrical steel
- an annealing of the punched parts from semi-processed magnetic steel.
These options were analysed and compared in cooperation with a lamp ballast manufacturer.
The respective studies of the influence of punching edges on the magnetic properties of electrical steel were carried out at strips and at magnet cores of inductive lamp ballasts. The specific length of the punching edges was
- s = 55m/kg for the strips (10mm*100mm)
- s = 90m/kg for the E-I-laminations (thickness d = 0.5mm).
The characteristic magnetic properties of the specimens were determined in the punching state and in the reannealed state again.
Investigations within the mini EPSTEIN-frame
Specimens 10mm*100 mm were examined. The magnetic characteristics of these were determined after cutting and again after re-annealing.
In the following diagrams some results of the measurements for specimens from M800-50A are represented. The magnetisability B(H) of the material is increased by the annealing and the specific total losses P are reduced.
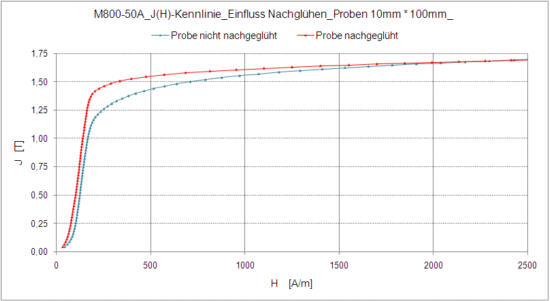

Investigations at magnet cores of lamp ballasts
Parallel to the measurements within the mini EPSTEIN-frame the effect of a re-annealing of punched parts on the magnetic characteristics of the cores of inductive ballasts was investigated.
For these investigations ballasts of different power were built up
- from not re-annealed E-I-stampings
- from re-annealed E-I-stampings
Despite the tensions by the packetising of the stampings the core-losses were approximately 20% smaller with the re-annealed laminations. For this reason possibilities were examined of increasing the operation polarisation J.
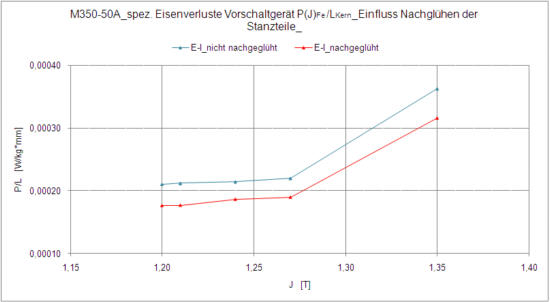
FEM Analysis
The described changes were investigated by a FEM-program.
It was supposed that the changes of the magnetic properties by punching are affected only in a narrow zone by b = 0.5 mm material-broad. For this zone of influence a reduced magnetisability B^(H^) was accepted. The transition to the uninfluenced material was modeled in the form of steps.
In the following diagram results of the FEM are represented.
The upper picture shows the material M350-50A without, the lower picture with a stress relieve annealing.
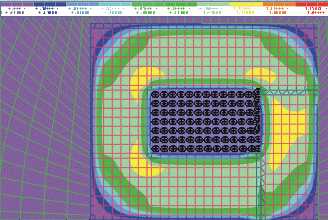
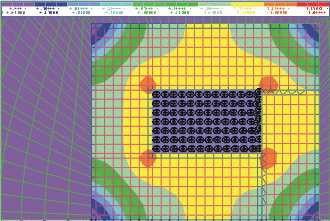
Summary
Changes of the magnetic characteristics of electrical steel by cutting/stamping and the influence of the magnetic fields in a magnet core are represented.
FEM – analysis in connection with magnetic measurements can be used during processing and solution of material-dependent optimization tasks and investment-relevant setting of tasks effectively (e.g. decisions on a stress relieve annealing of punched parts or on the substitution of finally annealed through semi finished electrical steel).
The changes
– of the magnetic properties of electrical steel by punching
– of the the fields in the magnetic circuit from punched laminations
were examined.
Such examinations are important to make a decision on material-dependent optimization tasks and on investment-relevant setting of tasks, e.g. a decision on a reheating of the laminations from finally annealed electrical steel or on the substitution of a finally annealed through a semi-processed electrical steel.